Why Glass-Ceramic is Best for Fire-Rated Applications
Safety is on the mind of builders and consumers as fire-related trends head in the wrong direction. According to data from the National Fire Protection Association, the number of fires has ticked up in the last couple years and losses have steadily increased for decades. On a macro level, the total number of fires is down 40-64% from 1980 for most major incident categories, but those fires are more dangerous. Property loss, adjusted for inflation, was 10% higher in 2020 than 1980.
As new structures are erected, it’s imperative to have the best materials available for fire-rated applications such as doors, building facades, roofs and partitions. Glass is commonly used because of its aesthetics and, depending on the type of glass, thermal resistance properties.
Two of the most common types of glass for fire-rated applications are soda-lime glass, a specialized, super-tempered glass, and glass-ceramics. There is, however, a stark difference between the ability to protect against smoke and flames between the two varieties of glass.
Glass-ceramic is scientifically proven to be superior in fire protection, which can help building owners limit losses. Additional benefits include agility for builders in installing the glass and reduced environmental effects when compared to other glass manufacturing.
Let’s take a deeper look at the composition of the two glass materials and why glass-ceramics is better suited for fire-rated applications.
Producing Soda-Lime Glass
The most common form of glass is soda-lime. Depending on the use, the material can be tempered to fit a specific function. For instance, its non-reactive properties make it suitable for protecting cold beverages and its relatively low melting temperature makes mass production cheaper.
The downfall of soda-lime glass in fire-rated applications is its very high coefficient of expansion. It reacts to thermal stress—expanding when heated, contracting when cooled—to the point where it often needs to be heat treated or tempered after it is cut to size for an opening. What this means for, say, a window, is that sun exposure can make the material so hot and expand so rapidly that it cracks.
Because of the high coefficient, soda-lime glass often has a difficult time passing testing for fire-rated applications. Many manufacturers send several panels to a certification facility and keep testing until one passes. They’ll use thicker glass in order to pass inspection, hoping it doesn’t crack in the 45-minute testing process, even though a glass that thick is not ideal for a fire-rated application and is difficult to install.
If the glass is set in a metal frame and the frame gets hot, the glass will also have hot spots, causing expansion inconsistencies within the pane. The annealing process—where each individual pane is met with incredibly high heat, then gradually cooled—introduces variations, too. Two soda-lime glass windows that were manufactured consecutively could have different finishes, thresholds for heat, and distortions. Window manufacturers can’t cut glass once it’s been tempered. The tempering process makes it such that a cut would shatter the glass pane into tiny fragments. Each pane must be ordered to size before it can be fit for its application.
Manufacturing Glass-Ceramics
Many of soda-lime glass’ shortcomings don’t apply to glass-ceramics. This type of glass has a virtual zero thermal coefficient of expansion. It can withstand fire tests up to three hours at 1,900 degrees C. and not crack. Glass-ceramic has no trouble passing fire tests.
The standard thickness of glass-ceramics is 3/16-inch, one quarter the thickness of typical soda lime glass being used for fire rated applications. Producing thinner glass consumes less energy than manufacturing 3/4-inch glass and doesn’t require polishing to eliminate defects or contain heavy metals such as arsenic, antimony and barium.
Builders and manufacturers may find glass-ceramics better to work with because they can acquire large sheets in bulk and cut the glass to custom sizes that fit an individual product or application. Glass-ceramics doesn’t require stress to be built into the material so it can be strong enough to withstand heat conditions.
Glass-ceramic is the same material that’s on stovetops, used daily in cooking applications, and has traditionally performed exceptionally well in the elements. It’s even used on spacecrafts to block ultraviolet light and protect photovoltaic cells. Here on Earth, it’s also the leading glass material for fire-rated applications.
What Fits for Fire-Rated Applications
Soda-lime glass may be the cheaper option, but for a negligible increase in manufacturing costs, glass-ceramics provide vastly superior safety performance in fire-rated and glazing applications at an optimal thickness and is easier to handle for builders.
Let’s say you’re installing a standard door with a glass pane that’s 26 inches by 76 inches. The pane is 123 pounds if it’s 3/4-inch-thick soda-lime glass. With glass-ceramic, the pane is only 3/16-inch thick and weighs merely 34 pounds.
Glass-ceramic material also prevents the spread of fire, hot gases and smoke for up to 90 minutes in windows and 180 minutes in doors. This proven superiority can help reduce the losses that fires have caused in recent years.
According to The American Institute of Architects (AIA), commercial construction is forecasted to rise 4.7% in 2022 over last year and increase by another 5.3% in 2023. As those projects come to fruition, glass-ceramics can represent a verified safety solution to keep buildings and building occupants protected from the risk that fires present.
About the Author:
Daniel Poling is a Fire Rated and Cover Glass Product Consultant at SCHOTT.
About the Author
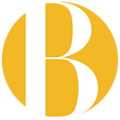
Contributed Author
BUILDINGS partners with industry experts to bring you contributed content covering the hot topics for building owners and facility professionals.