Acoustics Solutions: Ceiling is Believing at TURF Design
Near one of America’s busiest freeways in Chicago, an old, vacated firehouse with concrete floors and no acoustical elements was transformed into a thriving workplace by TURF Design, a company that creates customized acoustics solutions for facilities old and new.
Christoph Trappe stopped by to see their new headquarters.
[Begin transcript]
Christoph: Hello, everyone. It’s Christoph Trappe with interiors+sources and BUILDINGS.com. Thanks for joining us for another episode of our podcast. And today, I’m in Chicago at TURF Design at their new headquarters. Is that the right way to describe this building?
Zoe: Yeah. It’s our firehouse.
Christoph: It’s their firehouse. That was Zoe Post, who is an expert here on design. And we’ll chat. And I’m also joined by Dustin Headley. So, thanks for joining us today. We took a tour of the building already. Talk about the design, some of the history of the company and what makes you guys unique.
Zoe: Okay. We’re a new company, about two-and-a-half years old, and we are taking over in the design and acoustics industry, and architectural products. We have a lot of products that are aimed at both working in all types of spaces—branded environments, office spaces, schools—and we focus on a number of different things: design, ease of install, as well as…
Dustin: Adaptive solutions to custom spaces. Custom’s what we do.
Christoph: One thing that I noticed when I came in here, so I’ve obviously covered content around acoustics. And a lot of times, you either notice good acoustics or you don’t. Right? You walk in and sometimes I see a building and it looks beautiful and you walk in and their acoustics are terrible. But you can’t really tell until you walk in.
Right here, you have a very distinct branding. I walked in and I could tell, “Well, that’s TURF.” Right? So, talk about that. How did that happen? What’s the thinking behind the unique designs?
Zoe: Well, I like your take of kind of making something that’s not visible, visible. And we’re definitely doing that. Through all our products, all our products are helping with acoustics. This is a growing issue in open-office environments and schools. And we’re giving it a new edge, a new spin with creating solutions that are visually fun and visually work with the space.
BUILDINGS Podcast
Rather listen?
Put a Lid On It: Acoustics from TURF Design
Christoph Trappe speaks with TURF Design about their headquarters, products and how they help clients, “Put a lid on it.” Listen now >>
We work with architectural space. If there’s certain things that are going on in that space that we want our design to play to, we can work with that. So, our design is adaptive. Our products are products, but they’re flexible. They’re custom. We can make them work in a lot of different environments, under a lot of different types of constraints.
Christoph: So, we are in an open-office environment here, obviously. As you walk in and as we’re showing people your office here in our video especially, there’s walls between the spaces. There’s the design on top. Talk about how that helps with the work environment.
Dustin: What essentially is going on is the open-office. We actually tried to model the problem that we are trying to solve in the space that we are presenting the product in. Because in a lot of ways, this is acting as a showroom as well as an office. So, what we’ve done is, one, we sort of recreated the sort of typical office environment where you have people just running along, sitting in desks, working on designs. Very typical of an architecture office actually.
And then we tried to create a space that is both visually inspiring and also acoustically resolved in terms of its performance. So, looking at the way we treat the walls that are adjacent to the designers, so that sort of tactile adjacency is right there. I mean we’re in a space where it’s like we’re literally leaning against the felt. And then also, putting that up in the ceiling.
Being able to then also dynamically adjust that around things like lights, ductwork. It’s very common for us to move around sprinkler heads, truss structures and all of that. And then instead of making that feel like a collision of elements, making that feel fluid through the dynamic tools that we have. So, everything is parametric. It’s often driven by sort of surface development. And so, we draw the surface.
We sort of embed either the building code or the sort of field constraints associated with that and then extract out the geometries that will ultimately become the product. And in a lot of ways, it’s really interesting because literally what the architect can draw is exactly what they’re going to get in the instance of this. Along with a bunch of—should they need it, or should the project call for it, all this evaluation that can also be done.
So, we can very accurately control how much surface area we’re putting in this space. So, if we were to do an RT60 acoustics test, all of a sudden, we can know exactly what the impact on that space is going to be.
Christoph: We often talk about tenant amenities, right? People expect certain things. People expect good acoustics I would assume?
Dustin: Almost always. But it’s also not, like, a thing that you anticipate. It’s like one of those things that we end up—what’s interesting because when we first moved into the office, we didn’t have the ceiling and all the other amenities up.
And so, it was actually really difficult to work in the space. As we’ve actually worked and completed and resolved the projects that are associated and installed in the space, that has ameliorated a lot of the issues that people had and were complaining about when they initially moved in.
Christoph: So, in the open-office environment here, you actually worked here without good acoustics? Is that basically what you just said?
Zoe: Correct. Yeah. This room that we’re standing in was unusable. We’re standing in a small call room where you can break away from your desk, talk with one other person or just have some heads down time. It was unusable. It was concrete floor and two drywall walls. Now, there’s two felt walls on either side of us. And a series of baffles over our heads. And it’s almost like wearing ear muffs. It’s a nice acoustical environment. It’s very comfortable to be in this space.
Dustin: Yeah. I mean the way I would describe this space, there was like a second-and-a-half reverb time. So, if you can imagine that experience where in your cell phone where there’s a delay in your talking, it was exactly like that when we were initially moved into the space.
Christoph: I just got a headache just by that description.
Dustin: It was extremely bad and now it’s sort of great. These things sort of function and perform exactly the way we would anticipate it to work.
Christoph: Fantastic. So, as you’re walking to the open-office space, is there anything else you want to share about the design or the set up that would be of interest?
Dustin: I know there’s some dynamics with the VR stuff on this, but if you look at the installation that’s actually in the main office. One side of this is light gray and the other side is red. So, actually depending on the approach factor that you approach the installation from, you’re either going to get sort of a very potent visual statement from the color. And then from the other approach, you’re going to get a very subdued.
[Read also: Using Color in Your Wayfinding]
So, the view from the street is actually sort of the red, vibrant firehouse red. But actually, on the interior of the space, when you’re moving around the space, it’s more subdued, it’s lighter. So, we really tried to pay attention to the different features in the space and how people are going to experience it in the actual planning and design of the space itself.
Christoph: Very interesting. And then you have an adjacent room with the periodic table of TURF.
Zoe: Correct. Yeah, so next to our open office is a protype room where designers, as they’re working, can hop in there and use all kinds of different tools to create protypes of maybe semi-standard or totally custom products, a whole range of different things. Take photos, send them to architects or even physically send them to architects that they’re working with to proof out concepts. And also, just play.
So, it’s meant to be a space in which we can both work and test out both ideas that you’re working on in your projects and the ideas that you just want to try out.
Christoph: And then you can print.
Zoe: Correct. Yeah. So, we do have a host of other things that we do as well. We are able to—our production facility is actually not too far from here in a place where there’s a whole campus of different vendors that we work with directly.
Dustin: Yeah. The important thing to state here is we have a nice fabrication. There’s a vacuum form or a laser cutter or a 3D printer. And really the notion that we have with that is, at the manufacturing plant, we are either adjacent to or have that very same level of equipment for the large-scale stuff immediately accessible. And so, that manufacturing area in Elgin is adjacent to our partnered powder coater that’s a quarter-mile away or partner printing services that are a quarter-mile away.
So, it’s really—we’ve networked our way in the design industry in Chicago, but then also connected ourselves with the manufacturing blood of Chicago out in Elgin.
Christoph: And then as you walk upstairs, so you have similar design, even in the stairway going up. And then talk about the upstairs.
Zoe: Yeah. We tried to use every unique space. Since we want to be responding to different architectures, we want to be using all the spaces that are here available to us in the firehouse. So, we even work in the stairway. The upstairs is our flex space. There is a kitchen up there. We use it for different events and meetings, breakout team events that we need to be hosting.
We are a growing company, so there’s an eye towards that becoming office space in the future. On the ceiling, we have one of our standard products, which is a drop baffle. Once we put that install up, again, that was a room that transformed.
Right outside, we have one of the busiest freeways in the US, 90/94. If you could jump or put a really long ladder across, you could get to that freeway out one of the windows. So, it is right there, and you cannot hear any of it inside that office space.
Along one of the walls is also a printed adhesive wall that has a dynamic—it’s printed with a dynamic pattern that was created by two of our designers here, one of them Dustin, who worked to create—project a pattern onto a surface, assigned different colors to the different levels and create something with a lot of movement.
[Related: 5 Trending Tenant Amenity Ideas for Your Facility]
Dustin: Yeah. Really, not only speaking to our sort of capacities in terms of the printed felt, but that also speaks to a lot of the parametrics that we build here. Everything is custom. Any product that you might order from here is customizable through some parametric definition.
So, if you order a straight baffle, every time that we execute a project, it’s custom. It’s either standard custom or we’re implementing custom details, a custom arrangement, really trying to deal with what the architect has drawn, rationalizing that as close as we can relative to the product, and trying to deliver on basically what it is their vision is, trying to extend what it is they envisioned for this space, all the way through to a physical construction.
Christoph: And to get your product into a building, who do you normally work with?
Help BUILDINGS Shape 2019!
What BUILDINGS resources are most valuable to you? What would you like to see us provide?
Please take our short (under 2 minutes) survey - just 5 short questions.
Thank you!
Dustin: Contractors. Actually, one of my favorite set of humans, because I really enjoy people that build things, which is—I’m on the engineering side, so of course, I naturally am the one building a lot of stuff too. They’re a great set of humans to work with. And to that end, we also—a lot of the installation mechanisms and connection details that we’ve done, really trying to set up an ease of install scenario.
Our felt—if you can imagine installing 50 baffles along a 25-foot arrangement, basically laying up—instead of having to set pick points for each one of those cables, that would be a nightmare. Being able to set six to eight pick points for a Unistrut and then basically pop the baffles up in the ceiling, you can install an entire ceiling in a matter of hours.
Christoph: And we do hear that quite often, “the easier the better” for installation for sure.
Zoe: Correct. Yeah. We want installers to love us. So, they’re a huge target for us. Every one of our products we aim at having that ease of install factor. So, whether that be something that’s using our felt lock, which is literally popped in, or something that is using cable gripper or something else, it’s simple. It’s clean. And the design is seamless.
[Read also: Designing for Disaster with the Resilience Standard]
Dustin: And we’re also not afraid to go on-site to make sure things are perfect. I’ve been to at least two job sites this month. And just because there was a little bit of issues on-site with some things being installed out of spec, and basically, helping people out, making sure that everybody wins when these things are going on.
Christoph: And typically, other than the contractors, who decides to get your product into a building? And is it usually new construction or existing?
Zoe: Yeah. Usually it’s coming from architects. They are specking our products. And though we do have a host of other ways that we get projects, we do work with end-users as well. In those cases, we’re generally recommending an installer to work with alongside us.
Christoph: And of course, it can be existing buildings…
Zoe: Correct. For sure, yeah. That’s definitely one of our selling points is that we love t-grid.
Dustin: Well, but also, the story of this building is 120, right? 120-year-old building?
Zoe: Yeah.
Dustin: So, a lot of this, we—in order to actually execute some of the custom installations throughout, we had to laser measure internally (but we know some guys that can do it professionally, too) the spaces. And then actually we coordinated the product around what physically existed down to like about a ten-thousandth of an inch in some places.
Christoph: Very interesting. What else didn’t we cover that we should?
Zoe: The prototyping room. We better go in there and look at that periodic table of TURF.
Dustin: Yeah. I mean and also, a lot of the stuff is we really like to be challenged I think is one of the—sort of fantastic thing. We are really not afraid to custom. And that’s I think becoming more and more—we see that as an opportunity and a fun challenge. And we really embrace being approached by designers, contractors, everybody who’s just trying to figure something out to make the spaces and projects they’re working on more successful.
Christoph: Very interesting. Turf.design is your website.
Zoe: Correct.
Christoph: Were you involved at all in that decision to have “.design”?
Dustin: I wasn’t, no. Actually, the reason why I applied to the job is because of the clever stuff going on, on the website, so I wouldn’t be here if it wasn’t for both the “.design” and then that little logo dohicky that whenever you roll over it, it squash buckles.
Zoe: Flips around? Yeah.
Christoph: There was something else I saw on Instagram too. It said something like, “Turn down the noise” or something like that.
Dustin: Oh yeah.
Zoe: Yeah. We try to keep it clever and light.
Dustin: Ceiling is believing. Everything’s cheeky.
Zoe: Ceiling is believing.
Christoph: I did see that too. Great. Thanks everyone for joining us. Thanks for making the time, Zoe Post and Dustin Headley with TURF Design in Chicago.
Dustin: Thank you.
[End transcript]
Two handpicked articles to read next:
About the Author
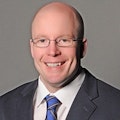
Christoph Trappe
Former Chief Content Officer
Christoph Trappe, a top 25 content marketer and author, was the former chief content officer at Stamats Communications, the parent company of BUILDINGS.