Dwell Time: Are Your Disinfectants Actually Working?
Time is valuable for your cleaning staff, and certain products can actually slow down their process.
How do they know they’re killing the germs they need to with their cleaning chemicals and disinfectants? It’s always pertinent to follow the suggested contact time of any product your cleaning staff uses.
In the disinfectant world, “contact time” refers to how long a product needs to sit and remain wet for it to kill the germs it’s meant to kill.
Disinfectant Dwell Time Risks
The most common disinfectants have a 10-minute contact time, which can present various risks, as does any long amount of contact time.
Patrick Kehoe, cleaning chemicals marketer for 3M, explains how consistently keeping a hard, non-porous surface wet such as floors can be problematic.
“Typical 10-minute contact time disinfectants pose a challenge to customers,” he says. “In normal HVAC settings, water can evaporate anywhere between six-and-a-half to eight minutes. Thus, keeping a surface wet (per the EPA registration guidelines) for 10 minutes could require a heavier initial application or the need to rewet the surface.”
Contact time is especially important for healthcare and education facilities.
“During last flu season, a number of schools closed their doors temporarily due to a high number of absences that were directly related to flu and other illnesses,” Kehoe explains. “Similar to healthcare, schools, colleges and universities are in the business of keeping attendance rates up.c
Related: Don’t Let Sick Building Syndrome Reduce Productivity
Liability is a huge risk, Kehoe adds, as well as not meeting the guidelines put forth by the EPA.
“There are a number of variables required for proper disinfection, and achieving the EPA required contact time is a part of the overall equation. Using EPA registered disinfectants in a manner different than directed is non-compliance but can call into question the efficacy of the product, and this unnecessary risk potentially bodes the question of ‘Are we killing the germs properly?’”
What to Consider When Deciding on Products
Kehoe says that to disinfect well, cleaning staff will always benefit more from a product that does the job quicker – but to keep in mind how the chemical interacts with a particular surface.
BUILDINGS Podcast
Pro Tips for Workplace Hygiene
Amna Handley, director of clinical development for Georgia-Pacific Professional, and Darin Squires, GP Pro’s general sales manager for commercial real estate, chat with editor-in-chief Janelle Penny about key hygiene concepts and how to help promote healthy work environments. Listen now >>
For example, bleach can be corrosive on floor finishes, as can any type of product with an aggressive PH level. Kehoe states surface compatibility is a crucial element when choosing the proper disinfectant. He adds that typically floor disinfection practices were only conducted if there was a blood or bodily fluid spill or reason for pathogen contamination.
“However, there are recent studies published that identify floors as risk areas,” Kehoe says. “Ultimately it is up to each facility to decide upon when to disinfect the floors, but using a quick contact time disinfectant that is safe for floors with a multi-application claim is crucial.”
Read also: Reduce Custodian Staff Turnover by Giving Thanks
To find the best product for your facility, Kehoe recommends first understanding how the product works – through information beyond a sell sheet.
“[Those] do a nice job of highlighting the main bullet points on products,” he says, “however, it’s important for decision makers to obtain the official technical documents, such as the product labels to ensure they review, select and use the disinfectants appropriately per the EPA.”
Make sure you’re using the product correctly.
Some products might need to be applied through spraying or need to be diluted a certain amount or mixed a certain way. It’s important to make sure you’re asking the right questions when choosing the most ideal disinfectant.
“We believe disinfection is more than just a chemical solution – it is a process,” Kehoe says. “It is critical that each facility review what is important to them and what their facilities need prior to reviewing, selecting and utilizing a disinfectant to help cleanse their facility.”
Two handpicked articles to read next:
About the Author
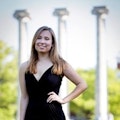
Sarah Kloepple
Associate Editor
Sarah joined the BUILDINGS team as an associate editor in August 2018. She is a graduate of the Missouri School of Journalism, where her focus was magazine writing. She's written and edited for numerous publications in her hometown of St. Louis.