It’s no surprise that packaged rooftop units (RTUs) are estimated to be the most widely used HVAC systems in commercial buildings. The space-saving design frees up square footage and keeps equipment out of sight. But that often means out of mind when it comes to maintenance.
The National Renewable Energy Laboratory (NREL) speculates that most RTUs are operating on a “run-to-failure” method devoid of preemptive or even routine maintenance. Low first costs and direct replacement system configurations simplifies RTU replacement and provides a relatively cost-efficient investment. Historically, these advantages have been viewed as providing a stronger ROI than adhering to an ongoing maintenance plan.
However, transitioning from this mindset to a preventative maintenance approach can extend the lifespan of an RTU to 15-20 years. Going a step further to incorporate smart controls, fault detection and strategic system enhancements can improve energy efficiency, reduce operational costs and minimize downtime.
With these figures taken into consideration, preventative maintenance can have a significant impact on your bottom line and preserve your RTU well beyond the minimum life expectancy.
Smarter Maintenance Moves to Make Now
Many manufacturers provide a preventative maintenance guide that includes recommendations to maintain highly engaged system components such as coils, filters and belts. Additional resources can be found from the DOE Better Buildings initiative including a field evaluation checklist that can be used to kick off a preventative maintenance program.
Among these critical parts, filters in particular provide an easy entry point to preventative maintenance. This is especially important if the system is operating with an economizer where outdoor air is being exchanged, or within a facility with high exposure to chemical off-gassing or particulate matter distribution. Both scenarios can degrade filters at an increased rate, leaving the entire system vulnerable to wear and obstruction. Faults of this nature cause the compressor to work harder and can result in a 5-10% increase in wasted energy.
Additionally, UV lights within the RTU can support improved maintenance outcomes. UV lights have long been recognized for reducing the circulation of airborne pathogens, allergens and VOCs. But they can also help to keep coils clean and prevent microbial growth within the RTU. This continuous cleaning via UV light improves system operation and reduces maintenance demands.
Merging Data and Maintenance
Research by the Department of Energy estimates that a well-implemented replacement or retrofit of an RTU with advanced controls can have a payback in just one to four years and a predictive maintenance program can yield a 25-30% cost savings year over year.
Advanced control options for RTUs include equipment-enabled smart controls, both as an independent system or integrated within a building automation system, and fault detection and diagnostics (FDD).
Smart controls use advanced sensors, programmable settings and remote management tools that can be integrated across multiple units and synced through multiple facility locations. Data is exported directly from the HVAC system to provide performance and operation insights that can be used to inform proactive maintenance and minimize downtime.
Additionally, maintenance schedules can be programmed into the system for a streamlined process between the facility manager and service contractors.
FDD further optimizes performance using a system of sensors that continuously monitor critical variables that affect operation and efficiency. Algorithms process this data and deliver alerts that allow facilities teams to pinpoint issues for fast resolve. And if service is required, FDD data can be remotely transmitted to the contractor before they arrive onsite to improve service efficiency and reduce downtime.
Although FDD is currently an optional system upgrade in most regions, newly developing energy codes such as California Title 24 are driving awareness and consideration for the technology, especially surrounding economizer efficiency.
Built for Maintenance
When system replacement is required, specifying an RTU with maintenance in mind from the start can go a long way in reducing lifecycle costs and extending the lifespan of the unit.
When specifying a new system, features such as service windows, internal lighting, condenser coil-cleaning hatches, airflow measurement stations, filter gauges, pressure transducers, and refrigerant shutoff valves simplify maintenance processes. System redundancies allow maintenance to take place without disrupting operation or requiring downtime. System redundancies such as multiple refrigerant circuits can help to reduce unwanted air conditioning down time. Blank sections can also be specified as a valuable advantage that provides space to enhance and retrofit the system over time without the need to find space within the ducts.
Additionally, specifying manufacturer-installed smart controls and using ASHRAE Guideline 36 standards, which will apply to RTUs in the future, to install and commission the unit will help ensure the system is protected and continues to run at optimum levels over time.
On their own, these RTU system features decrease downtime and allow service technicians to work faster. Combined with smart controls and FDD, the result is a full-circle ease of maintenance that extends rooftop unit system life and reduces repair and maintenance costs.
About the Authors:
Kevin Stockton is the director of Large RTU Product Management, Ducted Systems, for Johnson Controls. Jason Carter is the senior product manager, Ducted Systems, for Johnson Controls.
About the Author
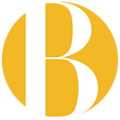
Contributed Author
BUILDINGS partners with industry experts to bring you contributed content covering the hot topics for building owners and facility professionals.