5 Trends in HVAC that are Improving Efficiency
Indoor comfort is paramount to running a building smoothly, and it’s driven by your HVAC system. But HVAC is a large – possibly your largest – consumer of your building’s energy. As a result, new trends and technologies in HVAC are turning their focus toward efficiency.
“Precision in controls has come a long way,” says Scott Janssen, energy engineering manager at JW Danforth, a mechanical contractor. “It’s giving everybody a lot more options in terms of how they want to use their space and the equipment.”
HVAC technology is becoming more sophisticated, built with better algorithms and able to gather more data. Janssen suggests one of the best ways to navigate the ever-evolving HVAC landscape as a facilities manager is to trust the program you’re using.
“Resist the urge to override some of the controls,” he explains. “A lot of building operators want to go in and customize things and override set points, but there can be unintended consequences with that. I think their best bet if they have a project where they’re changing their building, upgrading a control system – work closely with the controls contractor or whoever is setting up these systems to make sure they understand the way that your buildings are occupied, your schedules and what you want to accomplish.”
With that in mind, here are five trends in the HVAC industry that aim to help improve the efficiency of your building:
1. Smart Controls
HVAC controls are now being built with more precise sensors. There are better options for automatically controlled systems that are based on things like occupancy and the way the building is being used.
“Traditionally, you may have a control system [for] your HVAC system that might be set up according to the building operating schedule,” Janssen says. “That’s great, but in more recent years, you’re seeing a lot more sensors out in spaces gathering more information about what’s actually going on. And they’re doing a better job of identifying the level of activity that’s actually occurring in the building and then modulating the equipment.”
For example, CO2 sensors can use their occupancy information to appropriately ventilate a space as much as what’s required for that amount of people. “That’s a big energy saver,” Janssen says. “Smart controls have definitely come a long way. They’re only going to get better.”
Common Pitfalls of Installing HVAC Sensors
Even if you’ve selected the perfect HVAC sensor for your building, you won’t get a reliable measurement unless you install it correctly, explains Justin Walsh, an application sales engineer at Vaisala. “Precise measurement and control produces efficiency and promotes conservation,” he says.
Below are five common pitfalls to avoid when installing an HVAC sensor, as told by Walsh in this BUILDINGS Education course. (Watch it on demand here.)
1. Mounting a sensor in an area with restricted airflow.
Don’t install your sensor in places like behind a door or somewhere obstructed by other objects in the space. You want to choose a representative location with free airflow and away from sources of thermal interference. Place a sensor at respiratory height, usually between 4-6 feet.
2. Mounting a sensor near a heat source.
Make sure your sensor isn’t near any equipment that produces heat, such as a radiator, heating duct or even above an office printer or copier. Consider sunlight at all points during the day, and avoid placing it in direct sunlight.
3. Mounting a sensor sideways.
If mounted in this orientation, hot air won’t be able to escape. Any heat generated in electronics flows upward, so make sure your sensor is mounted in the correct orientation. When hot air escapes, fresh air can flow through. If it doesn’t, the reading will be at a higher temperature and lower humidity than it should be.
4. Mounting a sensor directly on concrete or steel.
These materials conduct heat and will act as a heat source for any sensors directly mounted on them. To avoid measurement errors, place insulation behind the sensor.
5. Mounting a sensor outside without proper requirements.
As outdoor sensors grow in popularity, be sure that, if you choose this option, you’re following the product requirements to keep it safe. Does it need to be shaded, shielded or vented?
One main challenge is measurements being affected by solar heat. Shield it with a reflector solar radiation shield, which can also function as a rain shield. Dirty shields absorb more heat, so make sure you clean it regularly. Mount it where the wind isn’t blocked. Walsh recommends mounting it on a northwest corner, to take advantage of the shade and wind. Don’t mount sensors under eaves.
2. Geothermal Systems
Instead of using oil or gas, geothermal heat pumps are fueled by the earth itself. They use the ground’s thermal energy year-round (since it remains consistent, compared to outdoors) to heat and cool a space.
Although the first cost for installing a geothermal system is higher than traditional HVAC equipment, Janssen says it pays for itself.
[Related: Smart Sensor Technology: Reducing HVAC Energy Use]
“In terms of efficiency and keeping things nice and comfortable in buildings, [geothermal systems] really limit the amount of mechanical equipment you’re going to have to have. If you’re designing a building you can have more space, because so much of your heating and cooling is being generated from the earth.”
Using renewable energy in general, Janssen adds, has grown significantly, as people become more environmentally conscious. “I think people are looking beyond the first cost. Sometimes that’s obviously a limiting factor. But I think people are more conscious of looking at the overall lifetime operating cost, the true cost of ownership over time. What are your maintenance costs, energy costs going to be?”
3. Integration
(Photo: In Buffalo, NY, 79 Perry Street has five Mitsubishi roof top units and a Captive Air Make Up air unit. Credit: JW Danforth)
4. Variable Speed Controls
Although HVAC equipment is traditionally designed to operate at peak load – the biggest expected heating or cooling load – it spends most of its time operating at part load. The industry, therefore, is seeing an uptick in more efficient variable speed controls.
[Related: 6 Tips to Improve Your Building’s Access Control System]
“There’s a lot of heating and cooling systems that may be fairly oversized because those peak loads are only happening a really small portion of the year,” Janssen explains. “Now, you’re seeing equipment that’s more right-sized for the applications, and it’s gotten very efficient at operating at those variable load conditions. So you’re seeing higher efficiency and less waste.”
BUILDINGS Education
Fine-Tuning HVAC Controls for Maximum Efficiency
A building control package is like a toolbox – it can’t help you if you don’t use it correctly.
Learn how to use every tool that a building control system gives you to reduce your energy costs. Find the best locations for sensors and switches to partially automate your control processes with zoning and setbacks.
5. Variable Refrigerant Flow (VRF) Systems
This type of HVAC system, as opposed to a traditional split AC system, has seen growth. Again, Janssen explains, they have a higher first cost but also have low ongoing energy and maintenance costs. VRF allows for an individual level of control, which can be appealing to your building occupants, Janssen says.
VRF also operates well in part load and can respond quickly when you’re coming out of a set point. For example, if over the weekend the building’s temperature was set back for the lack of occupancy, it can quickly return on Monday morning when people come back into the building.
Going Forward
As HVAC trends and technologies evolve, facilities managers will likely notice more moving parts and more predicative calculations. Janssen reiterates that it’s best to avoid overriding some of those parameters. Work with a controls contractor to flesh out any issues and consider retro commissioning if need be.
An overwritten system “may not be operating the way it was intended,” he explains, “so going back in and getting things back to the way they were – we always see a lot of potential there.”
Two handpicked articles to read next:
About the Author
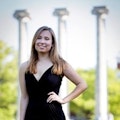
Sarah Kloepple
Associate Editor
Sarah joined the BUILDINGS team as an associate editor in August 2018. She is a graduate of the Missouri School of Journalism, where her focus was magazine writing. She's written and edited for numerous publications in her hometown of St. Louis.