One of the most important aspects of facility management is developing and maintaining a comprehensive safety plan.
Every company is built on employees, products and processes, but also strong departments that control operations, marketing and sales. But none of those can be successful without a workplace built around a sound safety protocol.
Why Safety Is Important
Safety systems are in place for a number of reasons. First, and most obvious, these plans are developed to protect employees in order to reduce or eliminate workplace injuries. Injuries stifle production and can lead to costly litigation, which in turn can also lead to turnover. None are good for productivity or the bottom line.
Second, damage caused by ineffective or non-existent safety protocols is a costly inhibitor to company growth. From warehouse storage incidents to forklift-pedestrian accidents to product damage, there are many issues that can be avoided by following the facility’s safety plan strictly to the letter.
Third, business insurance can become a problem to a company’s cash flow if it ends up increasing due to injuries in the workplace. Typically, claims history can stay active for three years or longer, meaning claims increases can affect a company for years. Lastly, if customers or even distributors find out about accidents due to safety issues, the company’s reputation can be damaged through social media or word-of-mouth discussions in the industry.
Common Safety Issues
Some of the most common safety issues occur in the areas where pedestrian employees and forklift traffic intersects. Marking these areas with floor signage will help designate separation, while busier areas can be split by safety fencing, edging or bollards.
Balconies and mezzanines are key areas that need to be protected to eliminate possibilities of falling as well as product and storage racks from falling on employees below. Mezzanine fencing with locking doors will help keep these areas secure.
Externally, docks are problem areas as the doors are always at risk for damage from trucks reversing. These areas need a set of separate safety products to protect, including safety netting, dock barriers and roll-up door protectors.
Interior Safety Best Practices
Aside from marking walking and driving lanes in warehouse facilities, other protocols should be set in place to ensure the safety plan’s effectiveness. Several companies manufacture stops—metal studs that when installed can actually stop a forklift from damaging a metal rack or entering a walkway. These are hugely important for safety protection.
While mezzanine protection is vital, so is education so that employees buy in to the importance of safety procedures—and this needs to target workers at all levels, including upper management.
Exterior Safety Best Practices
Bollards are the starting point for building any facility and installing exterior protection. These will protect dock traffic as well as separate vehicles from pedestrian walkways to and from the facility’s entrance and the employee parking lot. These are mainstays in front of every major chain retail store—Walmart, for example—but they are critically important to business-to-business facilities as well.
Exterior signage for trucking drop-offs is critical, especially with so many food deliveries being made to workplaces. Roll-up doors need protection from both dust and pollen, as well as rodents. The roll-up door protectors are similar to those that prevent air and dust from entering under doorways.
Roofs are not immune from protection either. There are a variety of pest control manufacturers that provide products to ensure rodents do not enter a facility—especially food processing plants—from the roof. Many of these newer products even include wireless transmitters that with Bluetooth activity can provide real-time notifications through smartphone apps.
How to Get Buy-In
Getting employees to be an active supporter of safety protocols is significant. It’s important that as new employees join the workplace, they receive messages stressing the importance of safety rules from fellow coworkers, not just the employee handbook or a supervisor.
One way to get these critical procedures top-of-mind and keep them there is to make it a part of daily employee life. Have a “Tip of the Day” focused on safety on each employee’s computer login screen. Then, start each meeting—whether company-wide gatherings or just small groups—with a safety reminder.
Rewarding employees for ideas that can improve the company’s safety plan is important as well. Get them thinking about it regularly. And then to keep the “safety train” in motion, get an employee from every department and create a safety committee to regularly address concerns and issues in the workplace.
About the Author:
Ken Arai is a market development specialist overseeing the door sweep division for Japanese-based Burrtec, a 60-year-old company that is one of the largest manufacturers of door protection products that keep rodents, dust, pollen, dirt and other unwanted items from entering facilities through openings under and around doorways. For more, visit www.burrtecusa.com.
About the Author
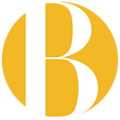
Contributed Author
BUILDINGS partners with industry experts to bring you contributed content covering the hot topics for building owners and facility professionals.