Strategies to Maximize Building Uptime with Fire Sprinkler System Connectivity
How much time do you spend thinking about your building’s fire sprinkler system? Chances are the answer is both not enough and more than you should. If your fire sprinkler system has been the cause of unplanned building repairs, you likely know the pain of getting a call about a frozen or broken pipe that’s caused a leak. You didn’t see the issue coming, and once it happened, you spent time you didn’t have to spare on the repairs.
What would it mean to you and your building operations to be able to avoid these calls (which often happen during off-hours) and save the time and expense of the repair? The cost of these unexpected issues can often be much greater than the repair itself. If you need to shut down operations, that can translate to huge business impacts.
Here are three key strategies to consider for keeping your fire sprinkler system healthy and maximizing your up-time:
- Keep up with your quarterly fire sprinkler system inspections, which are required per the NFPA (National Fire Protection Association) 25 “Standard for the Inspection, Testing, and Maintenance of Water-Based Fire Protection Systems.”
- Reduce risk of corrosion damage, which can lead to plugging problems, diminished fire sprinkler performance, water leak damage and reduced service life (which can all translate into significant risks to life safety, structural integrity and business continuity).
- Add connectivity to your fire sprinkler system to predict and prevent issues by helping you better understand the system’s health and address issues before they turn into larger problems.
These three strategies can provide a strong defense against unexpected, often expensive business interruptions, and they can build upon one another to optimize your system health while minimizing repair costs and downtime.
NFPA 25 sets the baseline for maintaining the integrity of your system. In addition to the same requirements of your monthly inspection of the fire valves and their gauges, your quarterly inspections add inspection of the water flow alarm, fire department connections and pressure control valves. These inspections are critical, but they only provide insight into your system at a specific point in time and can’t tell you what your system looks like on the inside.
Corrosion control measures can help you mitigate one of the major causes of sprinkler system issues. The interior of sprinkler system piping typically has all three components necessary for the chemical reaction that is corrosion: metal (black steel or galvanized pipe), water (either filling the pipes or moisture in the compressed air) and oxygen (trapped or compressed air in the system).
If you have a dry-pipe or pre-action fire sprinkler system with no water in the pipes, you can use nitrogen as the system air rather than oxygen to reduce corrosion. For your wet-pipe systems, consider a venting solution that removes trapped oxygen in the piping to reduce corrosion, or you can displace the oxygen with nitrogen to further fight corrosion and extend the life of the system.
Finally, there’s connectivity. Think back to that initial question: how much time do you spend thinking about your fire sprinkler system? With a connected fire sprinkler system, you have an assistant to do some of that thinking for you.
While not a silver bullet that will prevent all incidents, a connected solution can help “expect the unexpected” by keeping you informed in real time of your fire sprinkler system’s health. Sensors placed at strategic points on the system can measure variables such as temperature, pressure and water presence continuously. The data is sent to the cloud and can then notify the right people to act at the right time.
Imagine six weeks after your most recent quarterly inspection you have water collecting in your low points and the temperature is dropping rapidly. Everything looked great at your quarterly inspection but just a few weeks later you could be looking at a big issue—unless a temperature sensor alerts you to the impending freeze up before it happens.
How Do You Add Connectivity to Your System?
The latest connected fire sprinkler solutions utilize LoRa (short for Long Range) wireless technology. LoRa is a common wireless protocol ideal for use in buildings and campuses because it allows wireless signals to travel over long distances and through construction materials. It also operates on a quiet frequency band to minimize wireless interference from other devices.
Sensors placed throughout the system send regular updates to a gateway, which then sends the signal over a cellular network to the cloud. The network is also air gapped from your building network, separating it from your IT infrastructure.
The system collects the data and sends notifications when action is needed. The sensors are retrofit onto existing fire sprinkler system components and don’t change the way it operates. They’re add-on components that collect data about how the system is operating.
What is the Value of Predicting and Preventing Fire Sprinkler System Failures?
Getting in front of an issue and being able to better plan for repair costs is a primary benefit of a connected fire sprinkler system. This moves your sprinkler system maintenance plan from being reactive to predictive. Rather than absorbing the unexpected and often significant cost of repairs and downtime, your business can use digital tools to hopefully avoid those failures, understand when repairs are needed, and plan for the costs and time to do the repairs.
Facility managers can also better plan and prioritize day-to-day work with a system that tells them when there are potential issues requiring attention. For those operating a campus or multiple facilities, you can also get a full-portfolio view of system health. This helps focus time and budget dollars when prioritizing repairs and ongoing maintenance work.
Also consider your insurance premiums. If you could reduce the risk profile of your building or campus by avoiding fire sprinkler system failures, what would that be worth to your insurance company? Implementing a system that does just that gives you the ability to partner with your insurance company to potentially reduce your premium.
Finally, consider the mission and the role your building plays in achieving that mission.
For hospitals, a continuously functioning sprinkler system means minimized patient disruptions and logistical challenges. It also helps keep focus on the hospital’s mission: helping patients. A freeze-up or leak in your fire sprinkler system could destroy sensitive equipment such as MRI and x-ray machines, delaying patient care and incurring replacement costs. Canopies over emergency room and surgery center entrances can also be prone to freeze-up issues that shut down critical entry points, causing disruption and confusion for patients and staff. Preventing these issues can make a dramatic difference in the patient's experience.
For assisted living facilities, a connected solution means peace of mind and minimized disruption for residents. For hotels, it can mean events or conferences that aren’t interrupted or cancelled due to a sprinkler system issue. For sports stadiums, big games or concerts can avoid cancellation or rescheduling.
So, how do you know if a connected solution is right for your building or campus? If you’ve had a significant incident with your fire sprinkler system in the past, you likely can recognize the advantage in avoiding the issue altogether.
Consider a connected solution for helping supervise your sprinkler system if:
- You live in an area that can see frequent or unexpected freezing weather—even in the southern US, temperatures can suddenly reach freezing, leaving people unprepared and causing severe damage.
- Your properties have aging fire sprinkler systems, where corrosion is more likely.
- You manage multiple buildings or campuses and therefore, have a higher risk of an issue at any given one.
- Your property has had multiple system failures in the past and is seeing increasing insurance premiums and/or is at risk of losing coverage.
About the Author:
Aaron Jerabek is the Global Product Manager, Connected Devices and Services, for Johnson Controls. Aaron holds a Bachelor of Science in Mechanical Engineering (BSME), is a Six Sigma Blackbelt, and has over 20 years of experience in new product development, including 5+ in software. Learn more about predicting and preventing fire sprinkler system issues at www.johnsoncontrols.com/CFSS.
About the Author
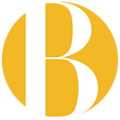
Contributed Author
BUILDINGS partners with industry experts to bring you contributed content covering the hot topics for building owners and facility professionals.